Bijlard actually produces things
Peter Bijlard is enthusiastic when talking about his company, which is located at the Platinastraat in Zoetermeer. Innovation is the main priority for this developer, manufacturer and distributor of glues and sealants for the professional market. “Our three laboratory technicians are always devising and developing new products and applications, while further improving our existing product range,” says Bijlard.Bijlard has been a genuine producer ever since 1956: everything devised in Zoetermeer has also been produced there. Some of the products are supplied directly to end users, while others are sold via intermediaries and retailers. In addition, around one hundred and fifty private label products are produced for third parties. Peter Bijlard responds with a smile, when asked about the quality of the range. “Oh, we almost never receive complaints, so I guess that says something about our products.”
Sustainability
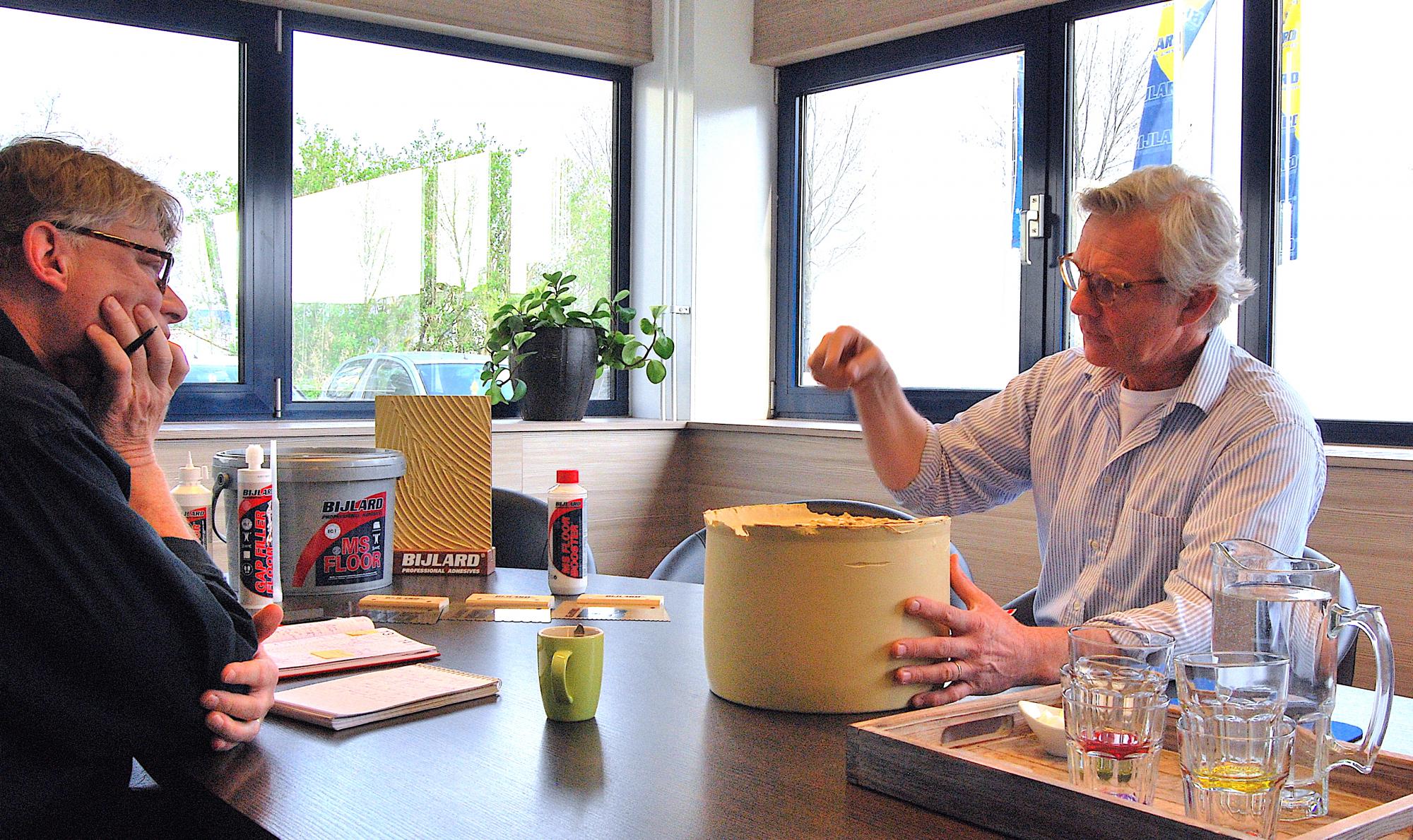
This philosophy was boosted in 2015 when the company won a so-called nano-voucher, which came with a cash prize. “The money is explicitly intended for research, and that's exactly what we did with it. Bijlard kicked off a process, which has actually not stopped since then. This involves working with TNO to conduct research into the use of nano technology in our products. In laymen's terms: you need between ten and twelve raw materials to produce glue. These products may tolerate each other perfectly at macro level, but could actually repel each other at nano level.
By using nano technology, we have been able to; for example, improve adhesion and UV resistance, while also realising better cohesion.”
A TNO audit is carried out every year, which Peter Bijlard describes as “rather intensive”, to demonstrate that the producer effectively masters the required procedures. “You can only conduct research with TNO, and use their knowledge and equipment, if this is the case.”
Innovations
New products can originate from a variety of routes. “Yes, that's true, but we have a top 3. Demand from the market continues to be important. For example: a new type of material becomes available, and it must be glued. We then work with the material to find the most compatible product. But we also develop products ourselves, based on our knowledge and experience. In this case, it is more supply-driven than demand-driven. ‘Discoveries’ in our lab, which occur almost spontaneously, are also very exciting. This involves devising and developing a solution, and then looking for potential uses. You could refer to this as the ‘serendipity’ category, which can be defined as finding something valuable, even though you weren't actually looking for it.”
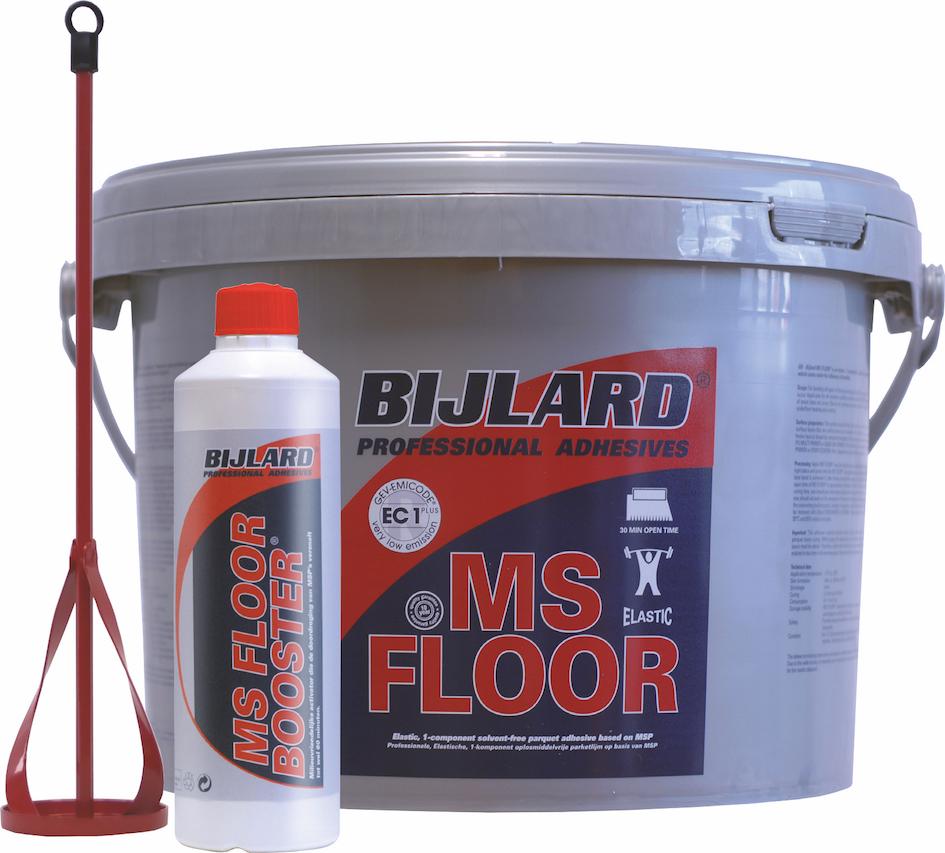
This article has been published in Parketblad edition 5. www.parketblad.nl
Date: 22-05-'18
< Back to overview